Make Your Own Cutting / Charcuterie Board
Save Money on a Beautiful Satisfying Project
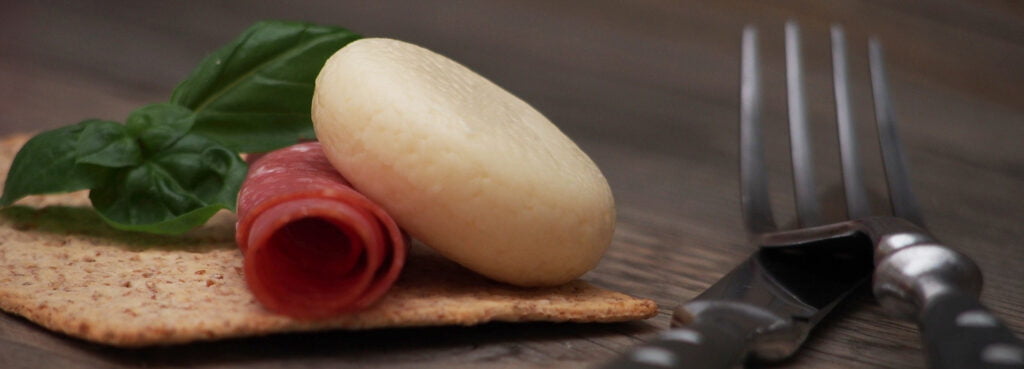
I don’t know about you, but I find it pretty hard to believe some of the retail prices of cutting boards, and especially ‘charcuterie boards.’ I guess that the oh-so-fancy term charcuterie necessitates a large accompanying surcharge. They’re like the Louis Vuitton handbags of the lumber world.
Don’t get me wrong, many of these things are beautiful. Some are intricately crafted by skilled artisans from fine materials. But most are just laminated boards (cutting boards), or somewhat pretty pieces of wood (charcuterie boards). Hopefully well finished (as we’ll discuss later). Big markup though. Massive.
It is easier just to buy one for sure, swallow the financial hit and move on. But think about the satisfaction of making your own, with your own bare hands, sourced from the very finest wood after an exhaustive search, to gaze lovingly and proudly upon with each use as you casually mention to guests that comment on its beauty “Where did I get that? Oh, I made it myself.”
Not trying to blow sunshine anywhere that it shouldn’t be here … admittedly most of your guests will greedily consume whatever fine foods you serve on your beautiful piece of art without a word of compliment, all while cutting cheeses and the like with much more force than necessary, needlessly scratching its delicately finished suraface ….
But now is not yet the time for bitterness …
Instead, let’s take a really quick look at the overall construction of a basic cutting board and charcuterie board:
So What's a Cutting Board Really All About?

Why not just cut any old board in to the appropriate size and be done with it? That would be fine. For a while. Totally go for that and move on if you like, that works. But, after a while, the board will eventually cup and start rocking around while you’re swinging your knife, and you’ll probably be losing fingers in the chaos before long.
Wood is a natural product and it moves around. Boards are cut with all sorts of different grain directions running through them, and the tensions in the board change when it’s cut from the trunk, and when it gets dried out after that, and when it gets wet again, and when the temperature changes…
You get the idea. Boards will cup. Get a nice flat board. Set it out in the sun on a hot day. Watch it cup.
So the usual way to deal with wood’s natural tendency to move around is to laminate multiple slices of wood together in an attempt to have each piece keep its neighbors in line and thereby keep the entire assembly more stable. Hence your industry standard laminated cutting board.
There’s a lot more that could be said on this topic, but I did promise to keep things brief for the moment. Suffice it to say that your standard store bought laminated cutting board will be made from pretty cheap stuff (some variety of wood unspecified on the label), but do its job well as per its tried and true design, all while looking fairly boring and setting you back a pretty penny.
What's a Charcuterie Board All About?

Essentially all those notions of trying to restrict our chunk of wood’s natural tendency to move around for improved cutting stability that we were so concerned about with out cutting board go out the window with our charcuterie board. We don’t want boring function any more, we want visual impact and lots of it. A wee little bit of rocking around from wood cupping be damned if that’s the cost.
What we want to do is to find some really cool looking slab of wood and serve the food on that. And cool looking pieces of wood aren’t neatly lined up and laminated for stability.
Of course there are exceptions. Cutting boards can be made to look cool, just as charcuterie boards can be made to look boring. Food can be chopped on a charcuterie board and then served on a cutting board.
But you get the idea.
Making Your Own Cutting Board:
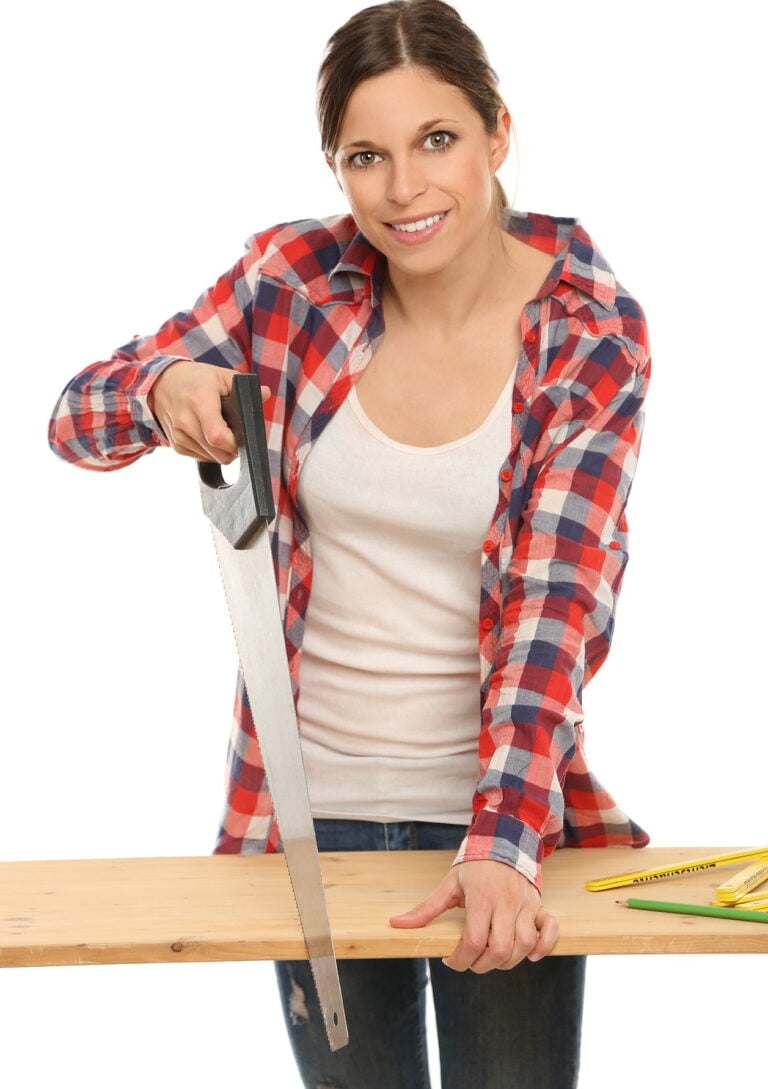
I may have to do a more detailed tutorial on this topic down the road one day, complete with an abundance of step-by-step illustrations and detailed discussions on wood theory. But for now I’ll assume that you, my beloved reader, have a basic knowledge of working with wood, and merely summarize the process. We’re talking here about making a simple laminated cutting board, not about the numerous possibilities for different fancier designs. So I’ll give you the basic summary and point out where you can expect the main challenges to lie.
Firstly, you’ll need to cut a number of wooden strips from a smooth faced board (or two). Each strip should be cut a bit longer than your desired cutting board length. They should be cut a teeny bit wider than you want your cutting board tall. And you need enough strips that the thickness of the board, multiplied by the number of strips, is a hair wider than your eventual cutting board width. Essentially you’ll be standing your little strips of wood on edge (from how they came off the board), and gluing them together that way. You’ll have to do the math for the required amount of lumber based on the size of cutting board you want to wind up with.
As an example, say I want an average sized cutting board of 14″ x 10″ and I’d like it to be about an inch tall. I decide that making it from cherry would be cool, and I know that my uncle has a stack of cherry boards in the rafters of his garage that have been there since the 70s. He will surely part with some of them in exchange for a six-pack each. How much beer will this project wind up running me?
On further investigation, I find out that his boards are all standard sized ‘one by six,’ eight feet long. Generally (and in my uncle’s case here), a ‘one by’ is actually 3/4″ thick and a ‘by six’ is 5 1/2″ wide. That’s because finished lumber (as opposed to rough lumber) is referred to by it’s ‘nominal dimensions’ before it’s planed to give it nice smooth sides and edges. Rough lumber is sized in actual size, but for some reason its thickness is always expressed in quarters, so a board two inches thick is called 8/4. Go figure. Were we to use rough lumber for our little cutting board project here, we’d have to smooth the faces flat (for gluing together) which would probably require access to a planer or some real hand tool chops.
I might have preferred slightly thicker boards to give me thicker slices accross my cutting board, but where else am I going to get cherry boards at a six-pack a piece? (That is a rhetorical question, lumber prices are kind of nuts lately). So I convince myself that 3/4″ slices will be awesome.
Harnessing the full undeniable power of mathematics, I determine that, to get a 10″ wide cutting board made from 3/4″ strips, I will need 13.33333333333….. pieces. At this point I am torn. Do I round down to 13 and get a slightly narrower cutting board, or go big and up it to 14. Boldly, I go to 14 strips.
My strips I know will be 3/4″ wide. Since I want my final cutting board to be about an inch tall, I figure that I will cut my strips to around 1 1/8″, leaving me some room to smooth out any unevenness after it gets glued up. I also know that my table saw blade is 1/8″ thick, so I will lose that much board per cut, requiring a total 1 1/4″ per slice. As each cherry board is 5 1/2 wide, I can get 4 slices across a board. At this stage I could decide to make the board a wee bit thicker to use that leftover 1/2″ of board that’s otherwise going to waste, but whatever.
So, 14″ long I said, hearkening back to the original master plan. I figure I will cut my strips to 15″, allowing for trimming after things get glued. I need 14 strips at 15″ long. And I can get 4 per 15″ piece of board. Dividing 14 by 4 and rounding up, I will require 4 15″ pieces of board. Forgetting for the moment about that pesky 1/8″ of saw kerf, I need 60″ of board, less than one of my uncles cherry boards.
This whole project is not going to set me back much more than a six pack. Beautiful.
Once you have your wooden strips ready, you’ll find a nice flat surface and cover that with waxed paper (so you don’t wind up gluing the whole thing to your preparation surface). You’ll line your strips up and cover the faces to be glued to their neighbors (both sides) with a thin but thorough coating of glue, then clamp them all together as straight as you can get them, until the glue dries. Larger projects can be clamped in sections, and then those sections later joined together if that’s easier depending on the scale of the cutting board.
After the glue has dried, you’ll sand or plane the faces flat, cut the ends to final length, round off your sharp edges, and add any other design features. Then you’ll probably want to apply a finish (more on that below).
And that, is the quick version of how you do that. Let’s not overthink this thing here, it’s not rocket science. Just be careful with the sharp tools when making it, and then of course the other sharp tools when using it.
If you were to cut your board in to short little pieces and orient them vertically to glue up, you would have an ‘end-grain cutting board.’ There are those who insist that this is the ultimate, and possibly even the only correct way to seriously orient cutting board wood. Not to inflame anyone’s emotions, but around here we believe that cats can be skinned in any number of valid ways. (Not that we’re inflaming emotions by skinning cats either – no actual cats have been harmed in the making of this tutorial!!!) The point is that you can cut things (not cats) on a slab of wood oriented in any direction really. Yes, even just that flat board if you like (just be careful about that oh-so-dangerous cupping that we’ve been discussing!)
In terms of wood, your best choice will be a relatively closed-grain hardwood (without many open pores to absorb errant liquids) such as maple, ash, cherry or walnut. You probably want to stay away from softwoods and more open-grained hardwoods such as oak. Of course there are lots of other options and also exceptions to every rule. One simple way to get fancy can be to use two (or more) different colored woods for your strips and arrange them in a creative pattern.
For glue you’re going to want a PVA wood glue along the lines of Titebond III, which is waterproof and FDA approved for indirect food contact. It’s essntially the gold standard of woodworking glues, probably the most popular glue there is for serious woodworkers. If you can’t get that don’t sweat it, really any standard wood glue will probably be fine.
Making Your Own Charcuterie Board:

The possibilities are really limitless for a beautiful charcuterie board, but essentially you typically want to start with a nice, really pretty, flat, chunk of wood. As per the conversation above, your dramatically figured board may not remain 100% flat over its lifetime, but here that isn’t as much of a big deal, because you’re sure not going to be vigorously chopping away on it!
And that is really about the gist of it. Go find a pretty board.
You can get a nice piece of wood in any number of places, but look up your local exotic wood dealer or specialty lumber yard if you have one nearby. You’re unlikely to find something great at a home center or chain hardware store. If you don’t have access to a physical store where you can see before you buy, then there are also lots of online vendors. Take your time and find something really special. Just make sure that the variety of wood you choose is safe for food contact (most will be).
If your wood has cracks or voids, they can be left as is, or filled with something, maybe colored epoxy. If you need to cut it size, go for it. Live edge, sawn edges, handles, integrated LED lighting, whatever, there really is no limit to your options. Queue the never-overused ‘the only limit is your imagination’ line.
Once you’re happy with your board, you’re going to want to sand it nice and smooth, probably through a succession of sanding grits, and then apply a finish to it to really bring out the character of the wood.
Finishing Your Cutting / Charcuterie Board:

No, you’re not quite done yet. Hold your horses.
There are quite a few options to putting a beautiful, food-safe, easy-to-apply finish on your board.
These include applying any of various oils, shellac, waxes, or even my special recipe homemade oil and wax blend that I keep a jar of around the kitchen for periodically sprucing up various wooden kitchen items, among other options.
There are so many options in fact, that although they’re all quite easy to apply, there is a bit to discuss. As this post has rambled on for a fair little while already though, I think it may be best to start a new page on the finishing (and refinishing) options for these and other kitchen wood items. So thanks for reading this far, and please join me in discussing How To Finish Or Refinish Your Cutting Board Or Your Charcuterie Board Or Various Other Of Your Wooden Kitchen Items.